Four Inspection Principles for Success: A Guide to Quality Assurance
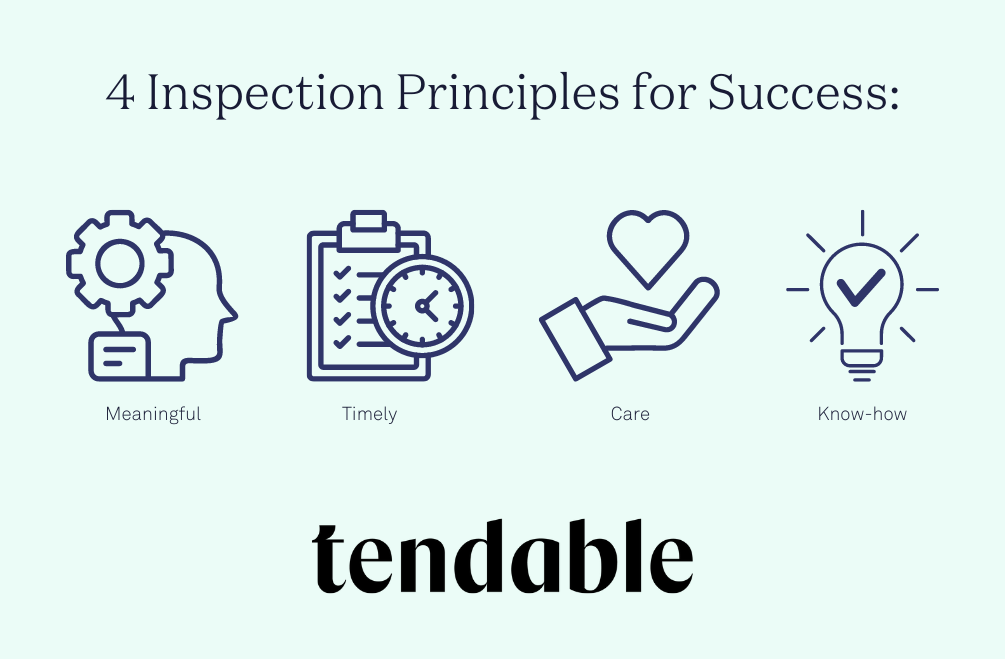
In the realm of quality assurance, inspections are a cornerstone for maintaining high standards and enabling continuous improvement. However, inspections often fall into the trap of becoming mere formalities - tick-box exercises with little real impact. To counter this, it's crucial to adopt a strategic approach that maximises the effectiveness of inspections. Here are four inspection principles that can help transform your quality assurance practices.
Make It Meaningful
Inspections should never be reduced to a simple check-the-box activity. To make inspections meaningful:
- Understand the Purpose: Be clear about why the inspection is being conducted. Each inspection should aim to uncover valuable insights that lead to tangible improvements through action.
- Maximise Observations: Take the time to observe thoroughly and note down all relevant findings. This comprehensive approach ensures that no critical detail is overlooked.
- Create Useful Actions: The ultimate goal of any inspection is to drive action. Translate your observations into specific, actionable tasks that address the issues identified.
By focusing on these elements, inspections become powerful tools for identifying areas for improvement and driving positive change.
Be Timely
Timeliness is a crucial factor in the success of inspections:
- Avoid Last-Minute Rush: Leaving inspections to the last minute often results in rushed and superficial evaluations. Plan your inspection schedule to allow ample time for thorough completion.
- Design Effective Schedules: Inspection schedules should be crafted to ensure that each inspection is conducted with the attention it deserves. Allocate sufficient time for preparation, execution, and follow-up.
- Allocate time to act on inspection findings: Your inspection schedule should also take into account the time required to amend any issues identified. This way, your inspections always serve the purpose of identifying improvement areas instead of just repeating existing issues.
Incorporating peer inspections into your routine can further enhance the process. Peer inspections, where colleagues inspect each other's departments or even different sites, bring fresh perspectives and insights. Tendable supports tagging of peer inspection activities, making it easy to integrate this practice into your workflow.
Spread the Love
Inspection responsibilities should not rest on the shoulders of only a few individuals. Distributing these duties widely has multiple benefits:
- Allocate Responsibilities Broadly: Assign inspection tasks to as many team members as possible. This not only lightens the load but also fosters a culture of collective responsibility.
- Encourage Ownership: Routinely assign actions to specific owners. Clear ownership encourages accountability and ensures that tasks are more likely to be completed effectively.
Clear communication of required actions is essential. Use the SMART framework (Specific, Measurable, Achievable, Relevant, and Time-Bound) to signpost what needs to be done, who needs to do it, and by when. This clarity helps action owners understand their responsibilities and the expectations placed upon them.
Know How You're Doing
Monitoring progress and understanding trends are critical for continuous improvement:
- Use Analytics: Platforms like Tendable offer powerful analytics tools that help track your successes and identify trends. Regularly reviewing these analytics provides valuable insights into your performance.
- Triangulate Data: Combine inspection data with other sources of information, such as incident management records and patient feedback. For example, if there is a trend of VTE (Venous Thromboembolism) incidents, reviewing inspection data on compliance can reveal underlying issues.
Adopting the Plan, Do, Study, Act (PDSA) cycle can enhance your action planning. This involves monitoring action plans, evidencing actions taken, and re-inspecting if necessary to ensure issues are resolved.
Conclusion
Building an effective inspection-based quality assurance program requires effort and strategic planning. By following these four principles - making inspections meaningful, being timely, spreading responsibilities, and continuously monitoring performance - you can enhance the impact of your inspections and drive substantial improvements.
If you’re looking to streamline your inspection process and make it more effective, consider exploring Tendable. With features designed to support these principles, Tendable can help you achieve your quality assurance goals.